August 17, 2023
Steps for Enhancing Cold Chain Assurance in the Biotech Industry
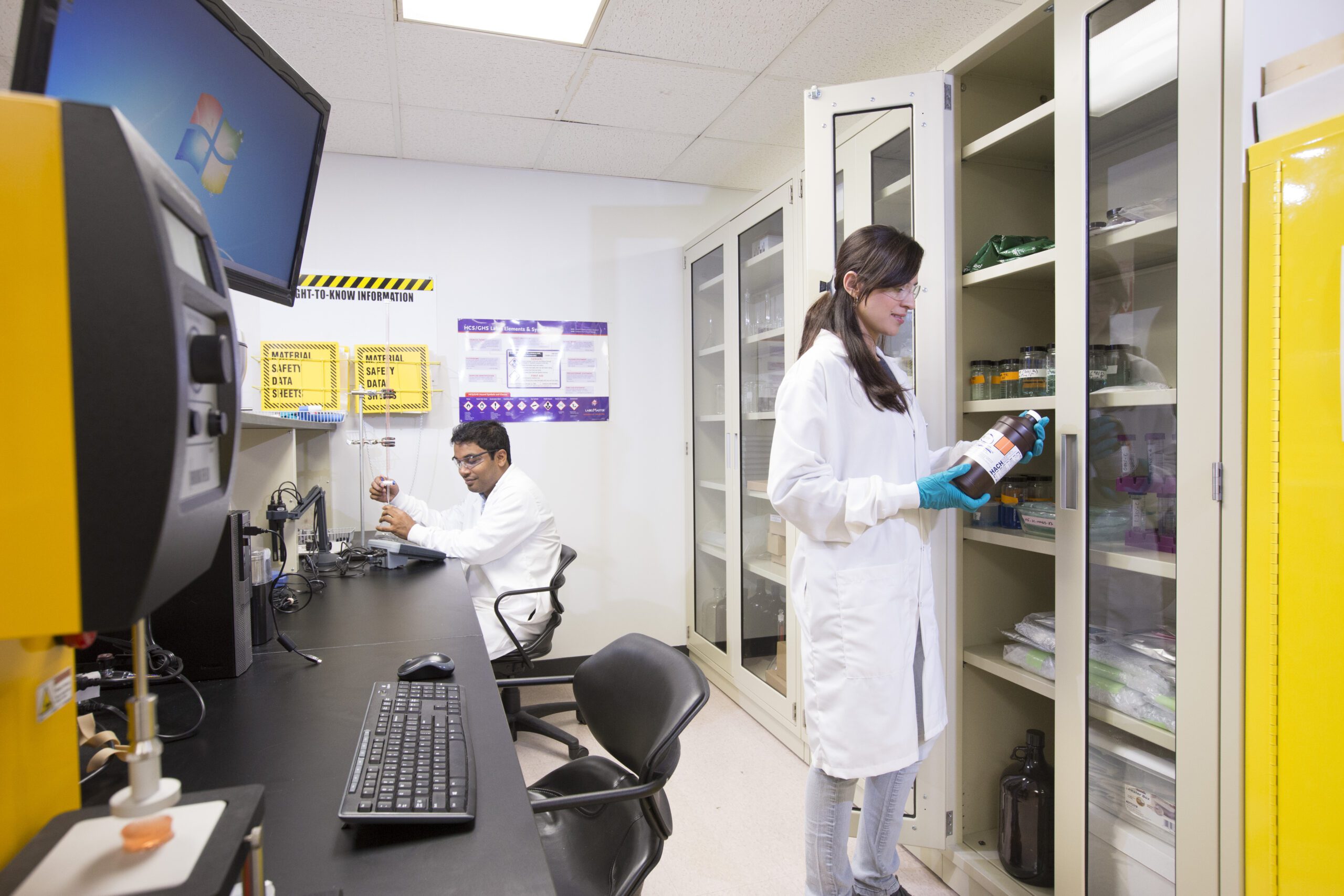
The importance of ensuring cold chain management for shipment of biologics and vaccines came to the forefront of public knowledge in 2020 during the rollout of the vaccines for COVID-19. Maintaining ideal pharmaceutical and biologics temperature throughout the cold chain is essential for product integrity, which, in turn, assures safe and effective delivery of therapy to patients. The market for vaccine cold-chain logistics is expected to reach $4.9 billion by 2030, and unfortunately, many vaccines today need to be discarded owing to a breakdown in cold chain logistics.
Cold chain management requires precise temperature control ranging from controlled room temperature (15°-25°C), refrigerated (2°-8°C) to ultra-low, cryogenic temperatures (-160° to -180°C)1. Storage requirement guidance is provided by the FDA in product labeling, Current Good Manufacturing Practice Regulations (CGMP), and by the U.S. Pharmacopeia (USP) 2.3. CGMP requirements apply not only to pharmacies, but also to pharmaceutical manufacturers, wholesalers and distributors, and shipping companies.
Here are some challenges and opportunities associated with cold chain management in the biotech industry:
Challenges
- Temperature excursions, where products are exposed to temperatures outside the recommended range, can occur during transportation, storage, or distribution. These excursions can compromise product quality and potency, leading to potential product wastage.
- The biotech industry is heavily regulated, and adherence to strict cold chain guidelines is required to meet regulatory requirements. Failure to comply with these regulations can result in product recalls, fines, or legal repercussions.
- In some regions, especially in developing countries or remote suburban areas, the infrastructure for maintaining a robust cold chain may be inadequate or unreliable, making it challenging to ensure product integrity.
- Implementing and maintaining a cold chain can be expensive, particularly for products that require extremely low or high temperatures. The cost of specialized equipment, monitoring systems, and transportation adds to the overall operational expenses.
- The biotech industry often involves global distribution, with products traversing long distances and various climates. Ensuring consistent temperature control across borders and different logistical networks can be complex.
- Continuous, real-time monitoring of temperature conditions is crucial to identify potential issues promptly. However, achieving real-time monitoring throughout the supply chain can be difficult, especially in remote or resource-constrained areas.
Improving cold chain transportation and storage in the biotech industry requires a comprehensive approach that addresses various aspects of the supply chain. Some key steps that can be taken to enhance cold chain management:
- Use qualified packaging and focus on sustainability. Utilize validated and qualified packaging solutions that provide reliable thermal protection for biotech products. Passive packaging systems and thermal insulating materials can help maintain the required temperature range.Incorporate eco-friendly and sustainable practices, including using energy-efficient transportation methods and recyclable or reusable packaging materials.
- Collaborate with experienced partners. Collaborating with reputable providers and 3PL (third-party logistics) companies can ensure proper handling and compliance throughout the supply chain.
- Invest in technology. Implement advanced temperature-monitoring technologies, such as IoT-enabled sensors and data loggers, to continuously monitor and track temperature conditions during transportation and storage. These technologies provide real-time data and alerts, enabling prompt action in case of temperature excursions. Leverage data analytics and AI to analyze temperature data, identify trends, and predict potential issues. This proactive approach can help optimize cold chain processes and reduce the likelihood of product quality issues.
- Establish Standard Operating Procedures (SOPs); train and educate personnel. These SOPs should cover all stages of transportation, storage, and distribution, outlining proper procedures for handling temperature-sensitive products. Properly train employees and stakeholders involved in cold chain management, including handling equipment and interpreting temperature data. Regular training sessions can reduce human errors and increase awareness of cold chain best practices.
- Compliance with regulatory standards. Ensure compliance with relevant regulatory guidelines and standards for cold chain management. Regularly update procedures to align with changing regulatory requirements.
- Validation, qualification and monitor KPIs. Regularly validate and qualify cold chain processes and equipment to ensure they meet industry and regulatory standards. This involves conducting temperature mapping studies, performance qualifications, and ongoing monitoring. Establish key performance indicators (KPIs) to measure the effectiveness of the cold chain. Continuously monitor these metrics and use the insights to make data-driven improvements.
By adopting these strategies and maintaining a strong focus on quality, compliance, and efficiency, the biotech industry can significantly improve cold chain transportation and storage, ensuring the safe and effective delivery of temperature-sensitive products to patients worldwide. This requires a partnership approach between biotech companies, cold chain solutions and service providers, and logistics providers, as well as leveraging technology and information to make meaningful progress.
Cold Chain Technologies and Biocom California are hosting an upcoming Lunch and Learn Event, which brings together experts in supply chain, logistics, quality, temperature control, packaging, distribution, and more for this one-day interactive workshop on October 17 in South San Francisco.
References:- Shelley S. Today’s pharma cold chain is going cryogenic. Pharmaceutical Commerce. Published September 25, 2020. Accessed April 16, 2023.
- US Food and Drug Administration. Current good manufacturing practice (CGMP) regulations. Accessed June 4, 2023.
- United States Pharmacopeial Convention. General chapter <659> packaging and storage requirements. USP 43–NF 38; 2020.